Retrouvez toutes les photos et vidéos dans la galerie
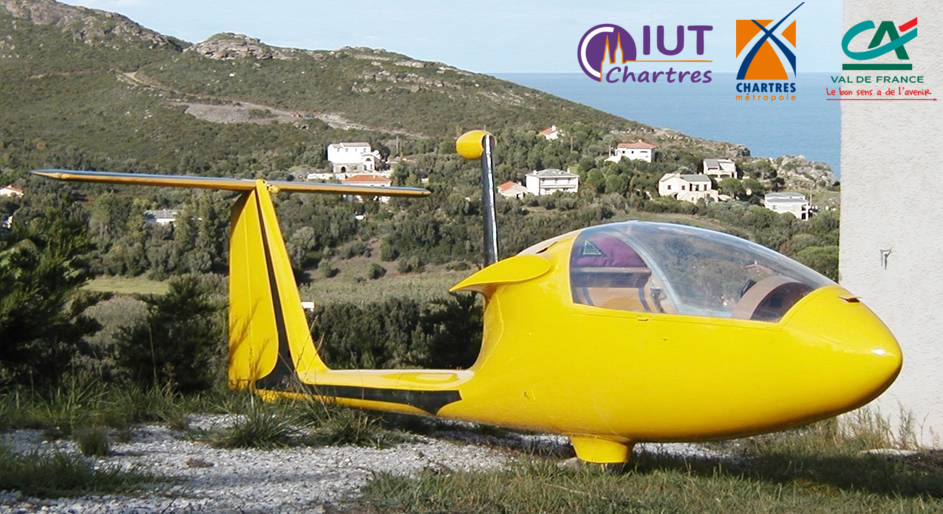
La genèse du projet
L'électroplane est un prototype de planeur motorisé développé par Clause Tisserand. Dès le départ Claude a conçu cet ULM 3-axe pour recevoir une motorisation électrique. Cette dernière permettra à l'appareil de décoller sans nécessiter l'intervention d'un remorqueur ou d'un treuil. L'un des avantages du planeur est le silence de celui-ci ce qui permet une pratique de ce sport sans occasionner de gènes sonores pour les riverains. Malheureusement, l'utilisation d'un remorqueur, motorisé celui-ci, induit beaucoup de bruit dans la phase de décollage du planeur. Les treuils sont quant-à-eux très couteux, et ne sont donc pas accessibles pour tous les aérodromes et sont d’une efficacité limitée. De plus l'utilisation de ces deux méthodes engendres une logistique plus complexe que pour la pratique de l'avion légère ou de l'ULM. On comprend ainsi toute l'utilité de l'utilisation d'une motorisation auxiliaire dans un planeur. On notera toutefois que ces avantages se font au détriment d'une perte de finesse de l'appareil mais qui peut rester raisonnable avec l'utilisation d'une motorisation légère.
La motorisation électrique présente alors ici tout son intérêt. Claude Tisserand a alors fait appel à AILEC pour réaliser la motorisation de son appareil. Le projet a démarré le 15 octobre 2016. Nous avons été chercher la cellule de l'appareil chez Daniel Dalby, également partenaire du projet, où elle était entreposée. Une remise en état de l'appareil et des essais moteurs sur banc de test sont actuellement en cours de réalisation.
La Cellule
Alors que de nombreux planeurs ULM possède un mat repliable le choix a été fixé à un mat fixe avec une hélice repliable. En effet, en vol et lorsque le moteur n’est pas en fonctionnement, l’ensemble mat-moteur-hélice ont une prise au vent importante et ajoute une trainée à l’appareil. La possibilité de rentrer le mat à l’intérieur de la cellule permet alors en générale de la supprimer. L’inconvenant d’un tel système est qu’il incorpore des éléments mécaniques ajoutant un poids important au système. La taille réduite d’un moteur électrique limite la prise au vent. Il a été déterminé par Claude qu’un mat fixe permet un gain de poids suffisamment important pour compenser la trainé induite par celui-ci.
Le choix de l’ensemble hélice-moteur et de son alimentation (batterie et contrôleur) est un élément particulièrement déterminant.
Essais de la chaine hélice-moteurs-contrôleurs-batterie
Fort de notre expérience sur les ULM électriques précédemment développés par AILEC, nous avons dans un premier temps sélectionné la solution optimale de chaine de traction adaptée à l’électroplane.
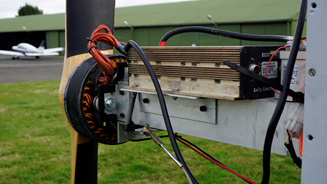
Sur banc d’essais statique nous avons réalisé différentes mesures (vitesses d’hélice, force de traction, puissance moteur, échauffements…) sur différents couple moteur/hélice afin de déterminer, pour un poids réduit, une force de traction adaptée au décollage de notre appareil.
La particularité d’un planeur est que le moteur est éteint durant la majeur partie du vol. Le poids de l’appareil, et donc de la batterie, a par conséquent un impact majeur. L’objectif que nous nous sommes fixés ici est de permettre à l’appareil d’effectuer un décollage depuis le sol, puis, d’effectuer une remonté après un temps de vol.
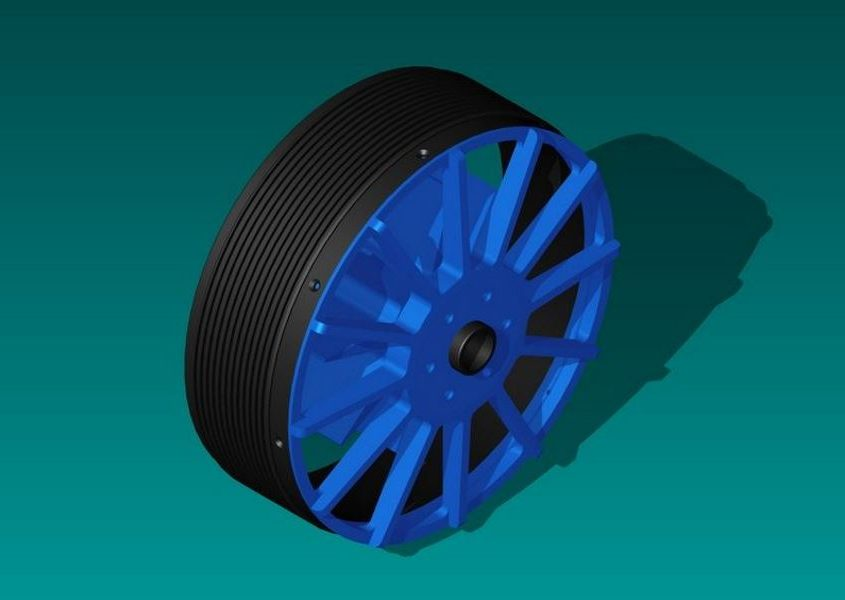
Le choix de la motorisation s’est donc porté sur un moteur électrique Rotex-Electric Rex 50 de 41 CV. Celui-ci est un moteur brushless (sans balais) construit sur une base en aluminium. Doté en outre d’aliments permanents néodyme, de fort rapport induction magnétique sur poids, sa faible taille et son faible poids le rends idéal pour un ULM. C’est ce même moteur qui avait été choisi pour notre Demoichellec et reste encore une fois la meilleure solution disponible sur le marché. Par ailleurs, son faible coefficient de caractéristique mécanique lui permet de tourner à basse vitesse augmentant ainsi le rendement de l’hélice, choisi de grand diamètre, sans nécessiter l’utilisation d’un réducteur qui est un élément lourd et encombrant. Ce dernier induirait un surcout en termes de poids et de trainé.
La réalisation de la batterie
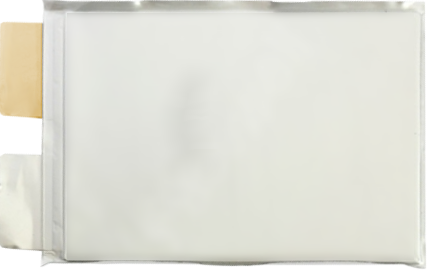
La batterie utilisée pour l’électroplane est constituée de cellules Lithium-Polymères 20Ah (voir photo ci-dessous). Cette technologie, utilisé dans les véhicules électriques moderne et reconnue pour leurs hautes capacités énergétiques pour un poids minimum (150Wh/Kg), est parfaitement adaptée à un planeur motorisé.
La batterie est constituée de 20 cellules pour atteindre une tension nominale de 74V et une capacité de 400Wh (Energie équivalente à 0,2L d’essence) offrant ainsi une puissance moyenne de 2,2 CV (1800W) pendant 15mn. Le poids des 20 cellules est d’environ 10 Kg et la puissance maximale délivré en continue peut atteindre jusqu’à 20 CV (soit environ 14,8kW).
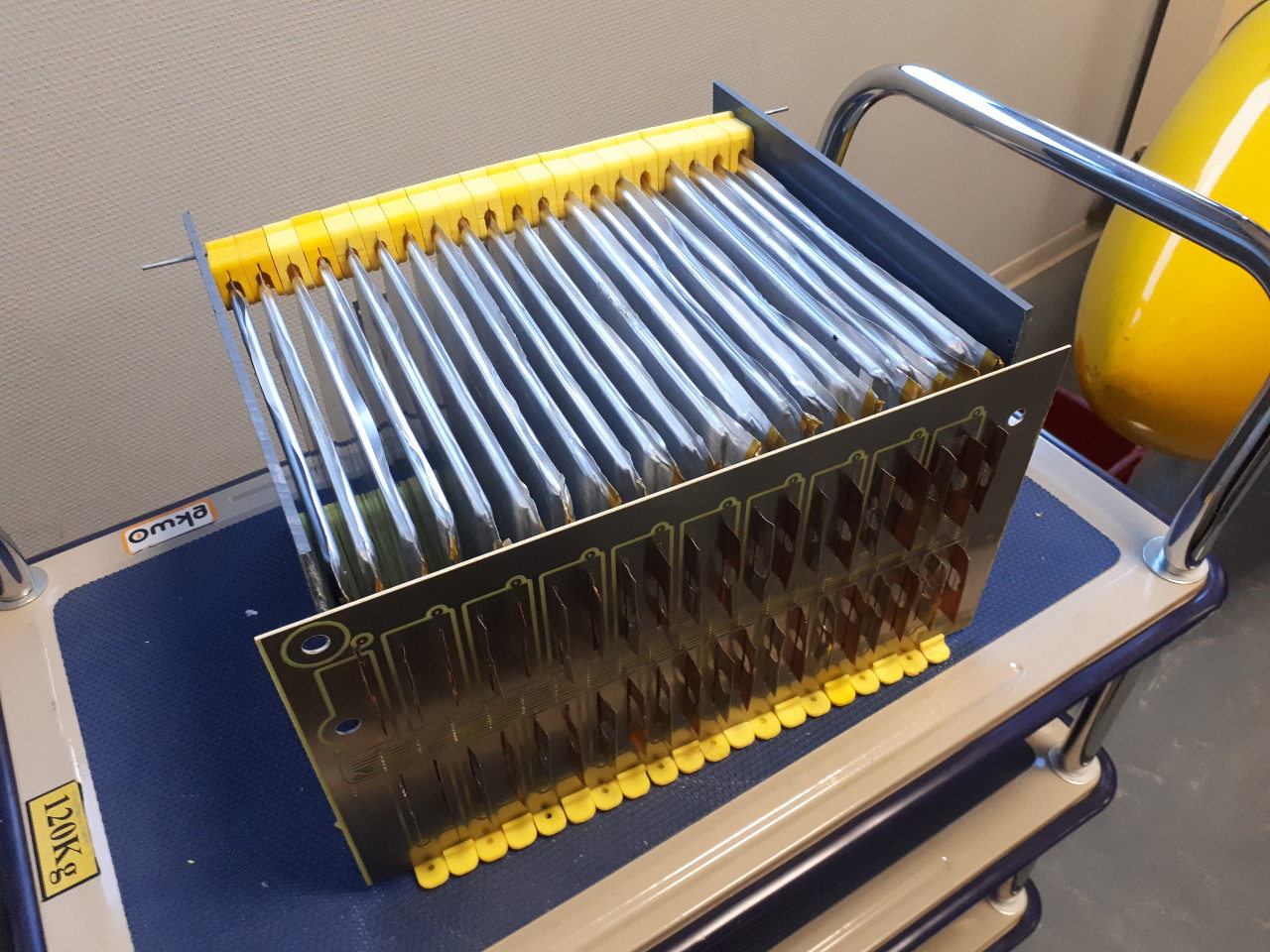
(en cours de réalisation)
Afin de garantir un maintien mécanique et une connexion électrique robuste de ses électrodes, les cellules doivent-être embarquées au sein d’un boitier. Celui-ci doit rester le plus léger possible et permettre une aération convenable des cellules (celle-ci émettent une chaleur importante en utilisation intensive). Ce boitier a été conçu et réalisé par imprimante 3D par notre équipe, comprenant un groupe d’étudiants de l’IUT de Chartres. Les cellules sont reliées entre-elles en série grâce à un circuit-imprimé conçus sur mesure.
Le volume de la batterie, placé au sein de la coque, n’est pas déterminant et il a donc été fait le choix de séparer les cellules d’un espace de quelque cm pour permettre une bonne aération.
Alors que les batteries fournissent une tension de 74V pour l’alimentation du moteur, un module d’alimentation développé par AILEC fournit des tensions auxiliaires de 5V et 12V pour l’alimentation de l’instrumentation.
L’instrumentation et le contrôle moteur
L’instrumentation de vol de l’électroplane est réalisée par des instruments de vol commerciaux : un badin, un accéléromètre vertical et un altimètre). La commande de la chaine de propulsion et l’instrumentation des paramètres électriques (courant, tension, puissance et énergie disponible) est quand-à-elle réalisée à l’aide de systèmes électroniques développés à l’IUT de Chartres :
- Le boitier de commande inclue le bouton de mise sous tension du système de puissance et la manette des gaz. Un afficheur LCD, supplémenté de deux voyants, permet en outre de contrôler en temps réel l’état du système et de vérifier la présence d’un défaut d’origine électrique (batterie vide, défaut du système de câblage, défaut moteur…). Le boitier a également été réalisé grâce à une imprimante 3D.
- Un boitier de distribution électrique permet l’interconnexion de l’ensemble des appareils électriques : batterie, contrôleur, instrumentation du cockpit et relais d’alimentation haute puissance.
- Un "cycle-analyst" est également implanté sur le tableau de bords affichant la puissance consommée et le niveau de charge de la batterie.
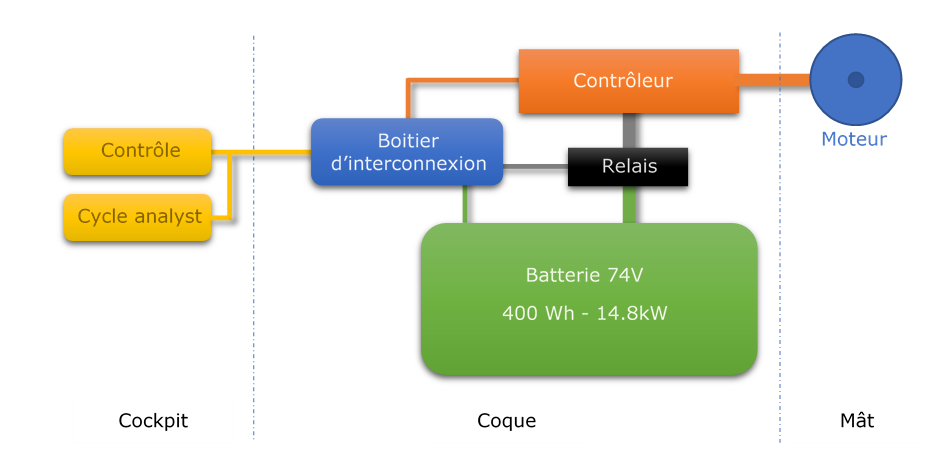
Représentation schématique du système de propulsion électrique
L’installation du système en cours de réalisation à l’IUT de Chartres.