Find all photos and videos in the gallery
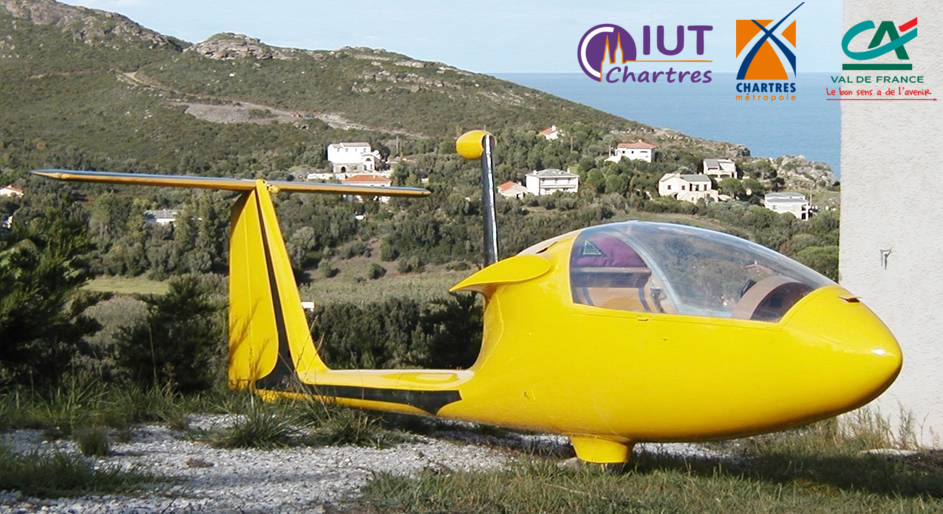
The genesis of the project
The electroplane is a motorized glider prototype developed by Clause Tisserand. From the start Claude designed this 3-axis ULM to receive an electric motor. This will allow the aircraft to take off without having to the intervention of a tug or a winch. One of the advantages of the glider is the silence of this one which allows a practice of this sport without causing of sound genes for local residents. Unfortunately, the use of a motorized remark causes a lot of noise during the take-off phase of the glider. The winches are very expensive and therefore not accessible for all aerodromes and are of limited effectiveness. Moreover, the use of these two methods result in a more complex logistics than for the practice of light airplanes or ULM. Thus, all the usefulness of using a motorization in a glider. It will be noted, however, that these advantages are at the expense of a loss of fineness of the apparatus but which can remain reasonable with the use of a light motorization.
The electric motorization here presents all its interest. Claude Tisserand contact AILEC to realize the motorization of its aircrafts. The project has started in October 15, 2016. We picked up the cell of the plane at Daniel Dalby, also partner of the project, where it was stored. A refurbishment of the aircraft and engine testing on a test bench is currently underway.
The cell
While many ULM gliders have a foldable matte the choice has been fixed to a fixed mast with a folding propeller. Indeed, in flight and when the engine is not in operation, the mat-motor-propeller assembly have a significant wind gain and adds a drag to the aircraft. The possibility of entering the mast inside the cell then allows in general to remove it. The disadvantage of such a system is that it incorporates mechanical elements adding a significant weight to the system. The small size of an electric motor limits the wind gain. It has been determined by Claude that a fixed mat allows a weight gain sufficiently large to compensate for the drag induced by it.
The choice of the propeller-motor unit and its power supply (battery and controller) is a particularly decisive element.
Tests of the propeller-motors-controllers-battery chain
With our experience on electric microlight previously developed by AILEC, we first selected the optimal traction chain solution adapted to the electroplane.
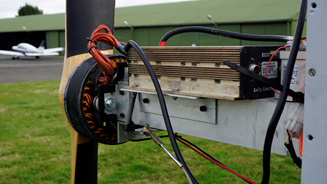
On a static test bench, we realized various measurements (propeller speeds, traction force, engine power, heating ...) on different engine / propeller torque in order to determine, for a reduced weight, a tensile force adapted to take-off. our device.
The particularity of a glider is that the engine is off during most of the flight. The weight of the device, and therefore the battery, has a major impact. The objective we have set here is to allow the aircraft to take off from the ground and then to recover after a flight time.
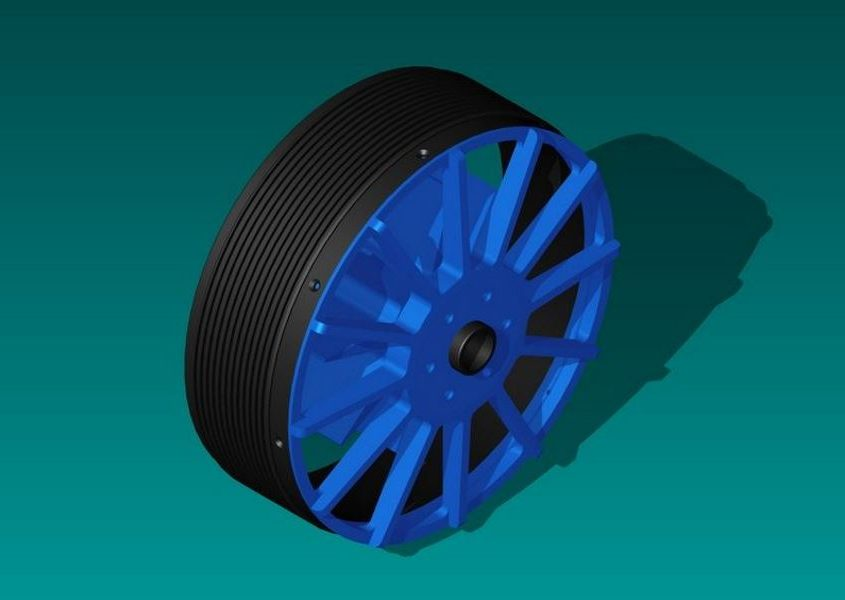
The choice of the engine was therefore a Rotex-Electric Rex 50 electric motor of 41 HP. This is a brushless motor (brushless) built on an aluminum base. Equipped with permanent neodymium feed, high magnetic induction ratio on weight, its small size and low weight make it ideal for an ultralight. This same engine was chosen for our Demoichellec and is still the best solution available on the market. Furthermore, its low coefficient of mechanical characteristic allows it to rotate at low speed thus increasing the efficiency of the propeller, selected large diameter, without requiring the use of a reducer which is a heavy and bulky item. The latter would induce a surcharge in terms of weight and drag.
The realization of the battery
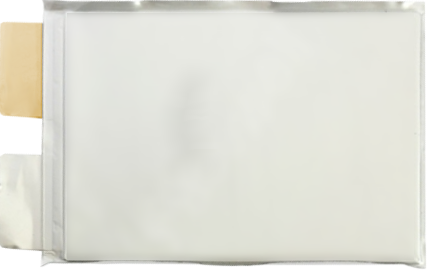
The battery used for the electroplane consists of 20Ah Lithium-Polymer cells (see photo below). This technology, used in modern electric vehicles and recognized for their high energy capacities for a minimum weight (150Wh / Kg), is perfectly adapted to a motorized glider.
The battery consists of 20 cells to reach a nominal voltage of 74V and a capacity of 400Wh (Energy equivalent to 0.2L of gasoline) thus offering an average power of 2.2 HP (1800W) for 15 minutes. The weight of the cells is about 10 kg and the maximum power delivered continuously can reach up to 20 CV (about 14.8 kW).
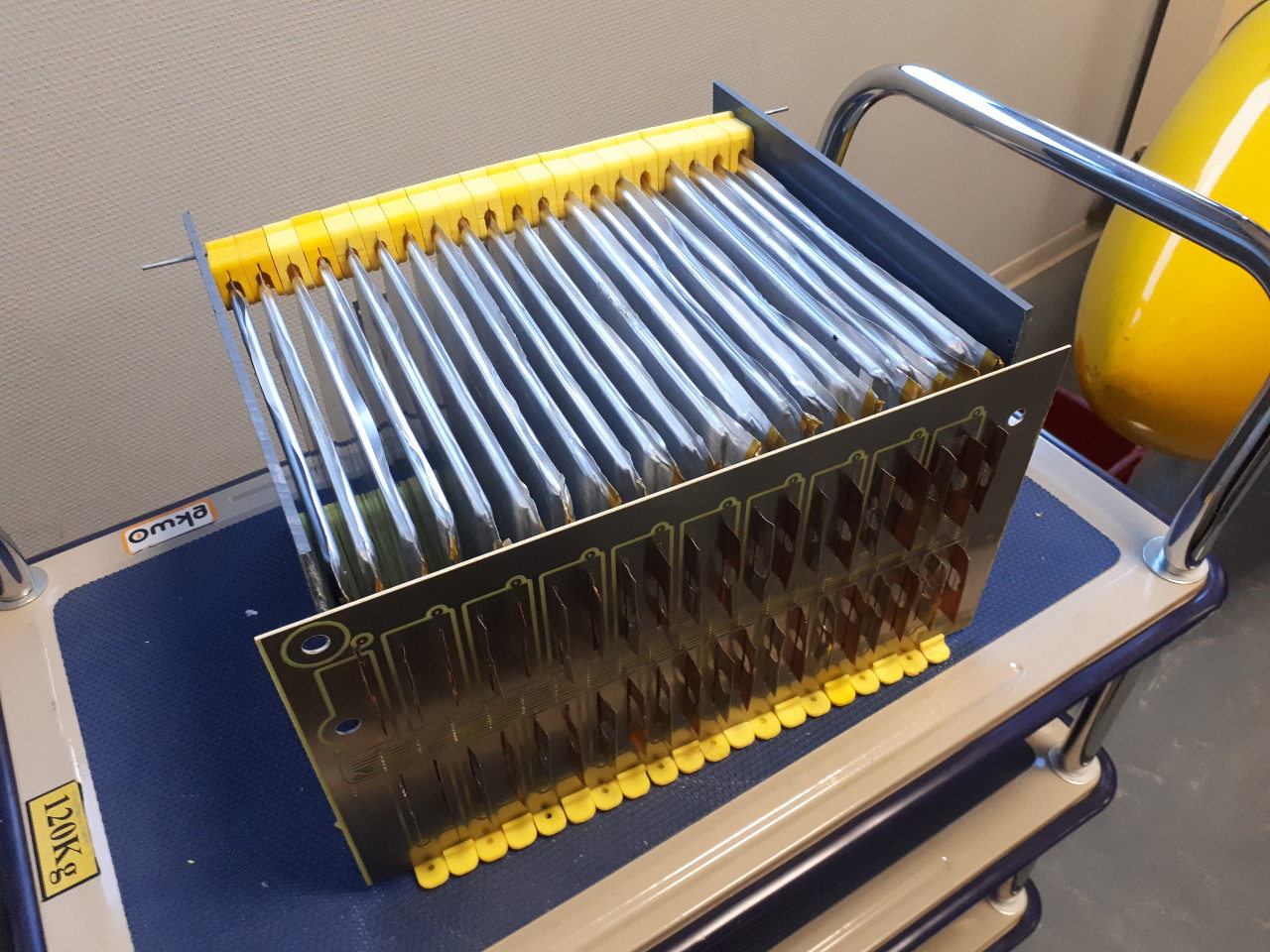
(in progress)
In order to guarantee a mechanical hold and a robust electrical connection of its electrodes, the cells must be embedded in a box. This should be kept as light as possible and allow proper ventilation of the cells (this emits a lot of heat during intensive use). This case was designed and made by 3D printer by our team, including a group of students from the IUT of Chartres. The cells are interconnected in series thanks to a circuit-printed custom designed.
The volume of the battery, placed within the box, is not critical and it was therefore decided to separate the cells of a space of a few centimeters to allow good aeration.
While the batteries provide a 74V voltage for the motor power supply, a power module developed by AILEC provides auxiliary voltages of 5V and 12V for powering the instrumentation.
Instrumentation and motor control
The flight instrumentation of the electroplane is carried out by commercial flight instruments: a joke, a vertical accelerometer and an altimeter). The control of the propulsion chain and the instrumentation of the electrical parameters (current, voltage, power and available energy) is done with the help of electronic systems developed at the IUT of Chartres:
- The control box includes the power system power button and the throttle. An LCD display, supplemented by two LEDs, also allows real-time monitoring of the system status and checking for the presence of an electrical fault (low level battery, fault in the wiring system, motor fault, etc.). The case was also realized thanks to a 3D printer.
- An electrical distribution box allows the interconnection of all electrical devices: battery, controller, cockpit instrumentation and high power power relay.
- A "cycle-analyst" is also installed on the dashboard showing the power consumed and the battery charge level.
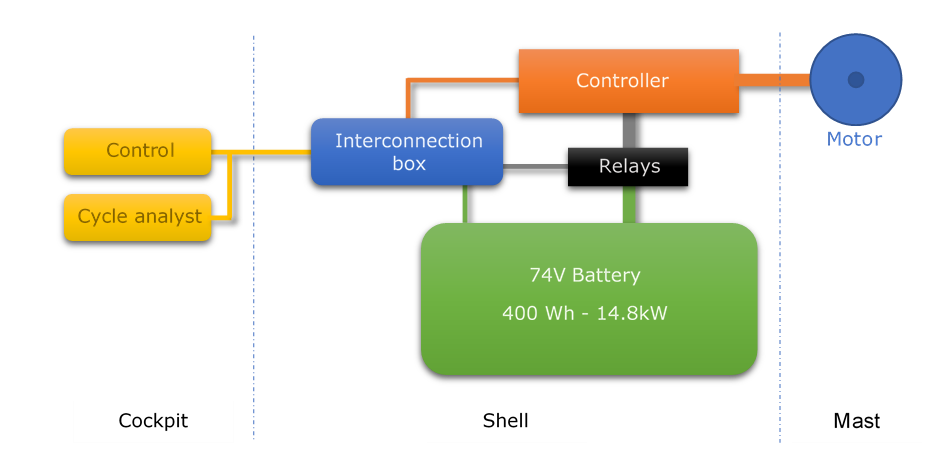
Schematic representation of the electric propulsion system
Installation of the system underway at the IUT of Chartres.